INTRODUÇÃO
Um cracker de gás da América Latina estava enfrentando vários problemas relacionados à separação de fases nos tambores de knock-out (KO) do Compressor de Gás de Carga (CGC), que afetava diretamente a qualidade da água de quench e a separação de hidrocarbonetos. A unidade processa Etano como matéria-prima, com capacidade para produzir 1.000 KTA de Eteno.
A DORF KETAL já era responsável pelo tratamento dos sistemas Água de Quench (QW) e Geração de Vapor de Diluição (DSG), e iniciou uma Análise de Causa Raiz com o cliente para entender e mitigar o problema.
DESCRIÇÃO DO PROCESSO E DECLARAÇÃO DO PROBLEMA
A Unidade possui um Compressor de cinco estágios, com a Torre Cáustica localizada na descarga do 4º estágio. A água e os hidrocarbonetos condensados retornam de todos os estágios para o vaso de knock-out do 1º estágio, onde a água é reencaminhada para a Torre de Água de Quench, sendo o hidrocarboneto encaminhado para tratamento. Desde a partida da Planta, a DORF KETAL vinha tratando o sistema de Água de Quench sem a necessidade de injeção contínua de quebrador de emulsão.
Após a substituição do Wash Oil injetado no Compressor para evitar polimerização, a qualidade da amostra de água de quench diminuiu significativamente, causando um aumento na saturação de pré-filtros e elementos coalescedores, bem como incrustações e corrosão sob depósito nos refervedores do DSG (Figura 1). Além dos custos operacionais mais altos, a Planta também não estava atendendo seus KPIs de eficiência, uma vez que a descarga (blow-down) do DSG era maior do que o projeto e era necessário adicionar vapor de caldeira complementar ao Vapor de Diluição produzido, devido à ineficiência dos refervedores.
Durante a análise de causa raiz, descobriu-se que o novo óleo de lavagem (wash-oil) consumido tem uma densidade relativa muito próxima à da água, criando um desafio para a separação de fases no vaso de knock-out. Com isso, a qualidade da água reencaminhada para a Torre de Água Quench diminuiu, criando uma emulsão intensa também no separador óleo/água. Por sua vez, o hidrocarboneto separado no tambor de knock-out também continha quantidades significativas de água, elevando o custo para o tratamento desta corrente.
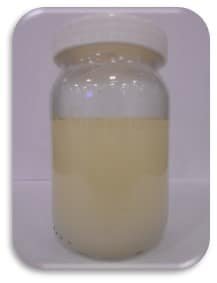
MITIGAÇÃO DE PROBLEMAS
Uma vez que a emulsão no tambor knock-out foi identificada, a Planta trabalhou em melhorias operacionais para o procedimento de drenagem de hidrocarbonetos. Na Figura 2, é apresentada a turbidez da amostra de água, antes e depois de feitas as melhorias operacionais. A aparência da amostra pode ser conferida na Figura 3.
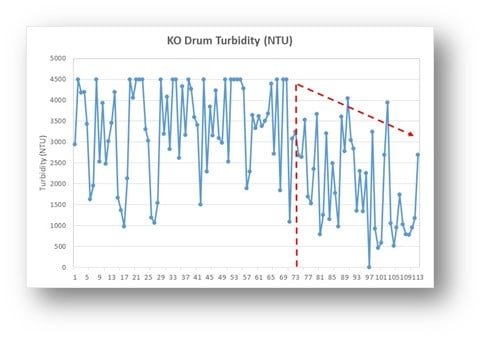
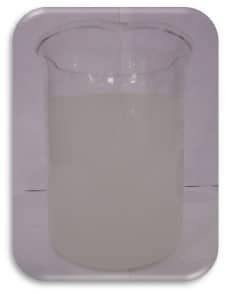
Mesmo após as melhorias operacionais, a separação no tambor knock-out ainda não era boa o suficiente para evitar prejuízos aos sistemas de Água de Quench e hidrocarbonetos. Assim, a DORF KETAL desenvolveu vários estudos de laboratório com amostras de campo para identificar um Reverse Breaker capaz de separar uma emulsão com dois fluxos de densidades muito próximas.
O reverse-breaker selecionado foi o DORF DA 2162B (Série BREAKPLUSTM), e o ponto de injeção recomendado foi o retorno do líquido do tambor knock-out do 2º estágio para o tambor knock-out do 1º estágio, onde ocorre a separação de fases.
O impacto na turbidez da água foi imediato após o início do tratamento com o produto DORF DA 2162B. Desde então, a turbidez foi mantida abaixo de 1000 NTU, significando quatro vezes menor do que o registrado (Figura 4). A aparência da amostra também é muito representativa da melhoria obtida pela adição do reverse breaker do DORF KETAL, como pode ser visto na Figura 5.
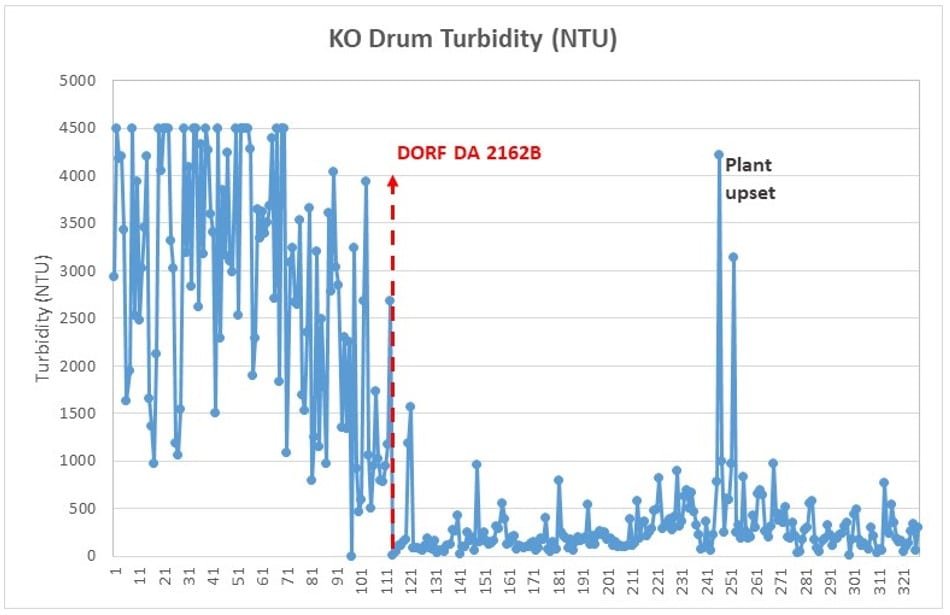
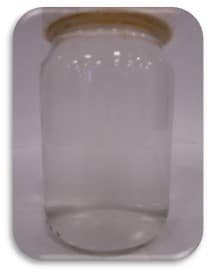
RETORNO DO INVESTIMENTO (ROI)
O tratamento de quebra de emulsão aplicado no tambor knock-out, usando o produto DORF DA 2162B, foi capaz de conferir diversos benefícios e economia à Planta. O investimento com o tratamento não só foi pago integralmente, como a Planta conseguiu economizar uma quantidade significativa de OPEX. Alguns dos itens de economia estão listados abaixo:
• Aumento do tempo de campanha dos filtros e elementos coalescedores (menos substituições);
• Redução dos custos de limpeza e manutenção dos refervedores DSG;
• Menor geração de efluentes na descarga de DSG;
• Redução da injeção de vapor de caldeira;
• Melhoria na operação do sistema de hidrocarbonetos, reduzindo a quantidade de água separada e a necessidade de seu tratamento externo.
Além dos itens descritos, é fundamental destacar que diversos aspectos relacionados à exposição de pessoal e ambiental também foram aprimorados, uma vez que a geração de efluentes da Planta foi significativamente reduzida, bem como as intervenções no processo (pré-filtros, filtros, trocadores de calor, etc.)
O trabalho de parceria entre o cliente e a DORF KETAL foi um ponto fundamental para este resultado de sucesso, combinando os esforços operacionais e químicos para alcançar e superar os KPIs estabelecidos.